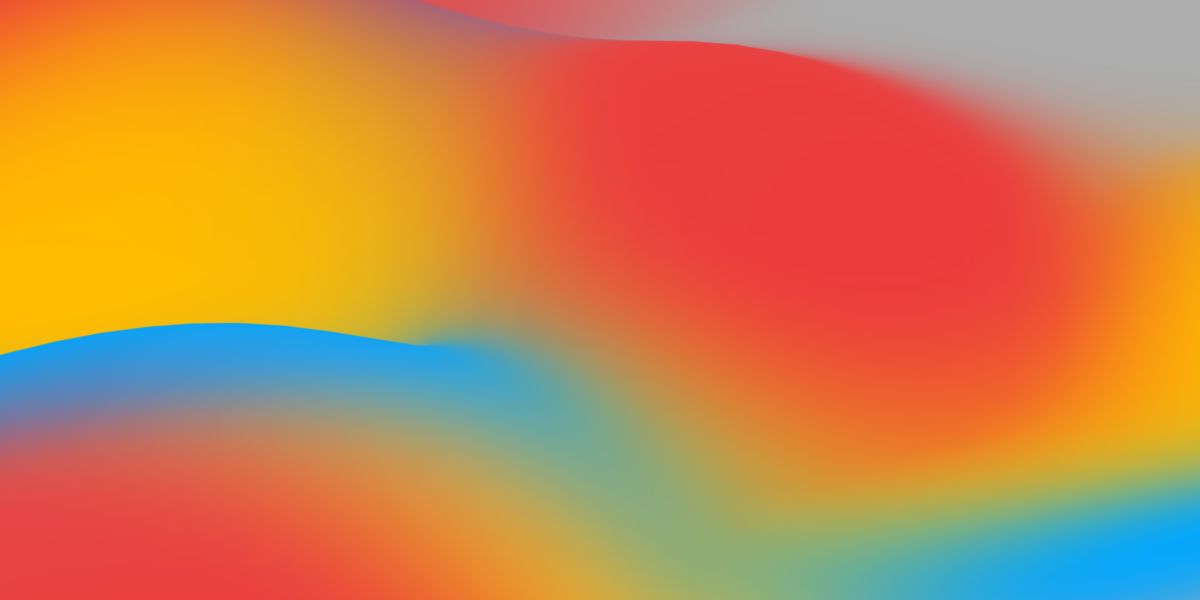
Inovyn Goes Digital to Manage Incidents and Change. Reports an Incident in Less than 10 Seconds
Inovyn is a vinyl producer that ranks in top three worldwide. The company has more than 4,300 employees and is active in ten countries across Europe. Wholly owned by Ineos, one of the world’s largest chemicals companies, Inovyn’s activity is building a world scale business that continues to serve its customers and rapidly responds to changing European markets. Annual production volumes are exceeding 40 million tons.
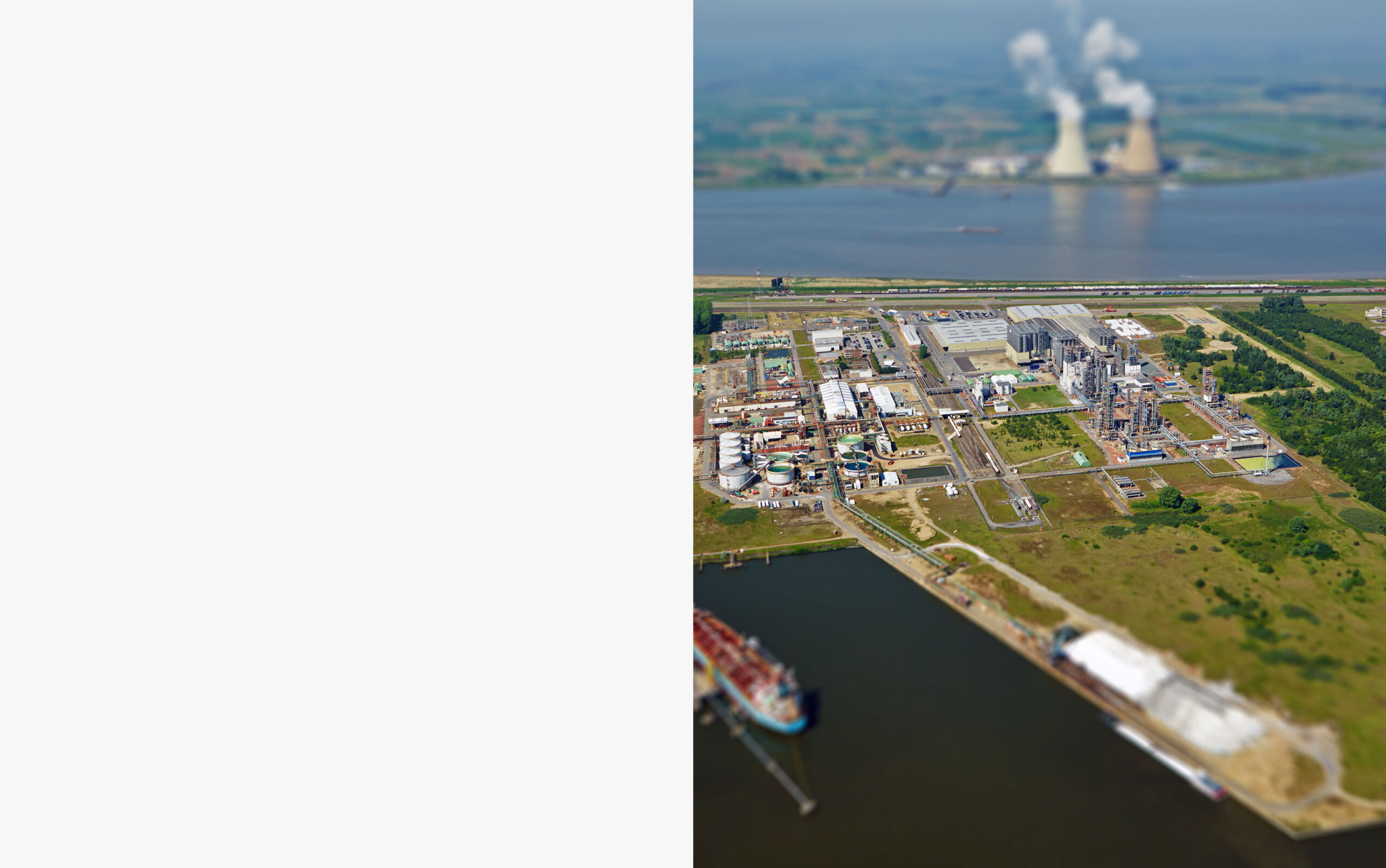
In A Nutshell
Inovyn was seeking a solution that could ensure workers’ safety, efficient action and incident tracking, and compliance with legislation. They also needed a suitable system to manage changes following a structured method and a well-defined process.
TenForce’s specialists have a very good understanding of the industry. During the implementation of the Incidents Management, Action Management and Management of Change modules, we did an internal audit to establish the normal processes in our organization and then TenForce took the lead and worked it out.
DIRK GYZELS
HSEQ AND FACILITY MANAGER INOVYN MANUFACTURING BELGIUM
After having decided internally what were the regular processes and workflows for the organization, Inovyn set off adopting TenForce Incidents Management and Action Management modules. The Management of Change module later integrated naturally in the system. Inovyn’s stakeholders and TenForce’s specialists worked together to customize the platform based on the client’s needs. Now employees from all levels in the company use the modules on a day to day basis, enjoying the benefits of a modern scalable EHS platform.
A changing world and increasing demands that soon proved to put a strain on teams
Obsolete tools for a modern workflow
Before adopting TenForce, Inovyn was struggling to record incidents, plan follow-up actions and start managing changes using aging tools such as handwritten forms, Excel spreadsheets, separate Word documents, and SharePoint environments. It was a time-consuming process and operators were having trouble tracking activities and quickly responding to incident-related processes.
Increasing load of mandatory reporting
In the beginning of their activities, Inovyn didn’t have too much trouble reporting to authorities and governments in their countries of operation. But as soon as the obligation to submit reports increased, the company management felt overwhelmed and needed a central system for official and technical records, to comply with requirements from ISO, OSHA and other regulatory bodies. There was a general state of uncertainty over satisfactory EHS compliance during audits.
Inconsistent collaboration
With data scattered in emails, paper documents and aging systems, improving data traceability and keeping a clean audit trail was an important necessity. The need for visibility of actions was crucial and Inovyn was also struggling with getting their employees to address tasks in a timely manner and using a common platform. There was also a strong demand to have an overview of the complexity of all requested and ongoing changes.
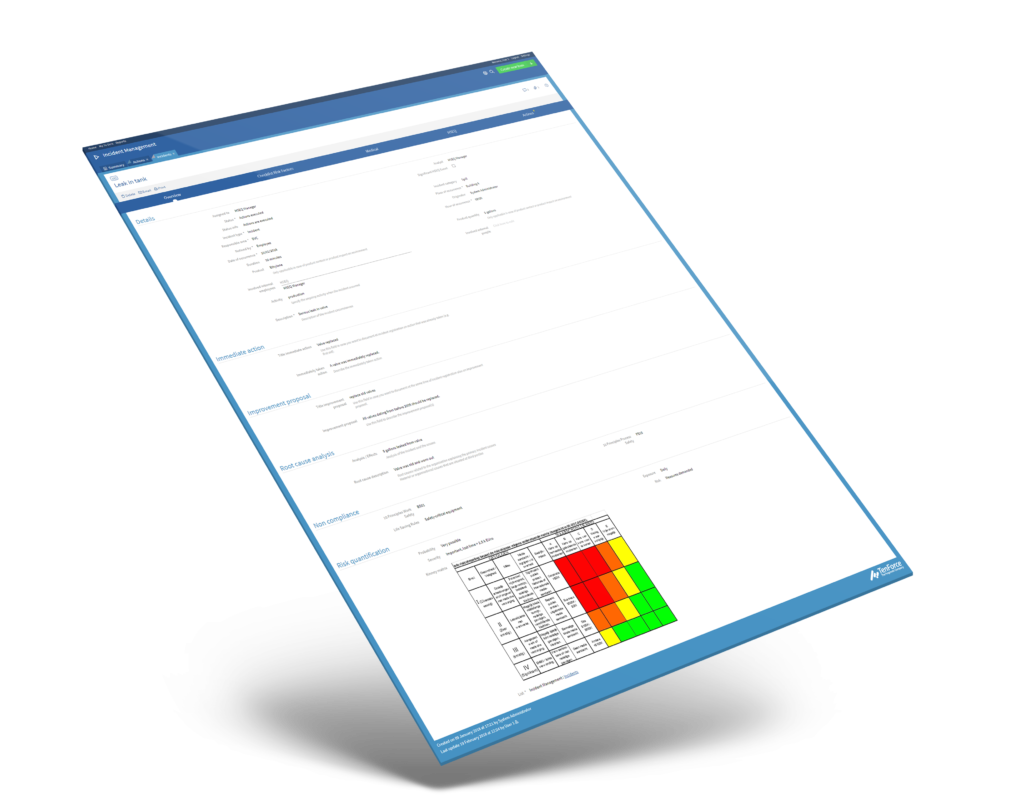
Adopting a Digital Enterprise-Wide System to Manage Incidents, Audits, Change and Actions
In an effort led by their Operations Manager to replace Excel spreadsheets with a modern digital tool, and after exploring the market, Inovyn found that TenForce was the best answer to their challenges. In 2012, Inovyn adopted the Incidents Management module. The upgrade made internal and external audits a task easier to handle.
Operators became able to capture, track, investigate and report incidents using one enterprise-wide system, standardized digital forms and not pen and paper. The follow-up is very important, to solve reported incidents and defining CAPAs is a TenForce feature now helping Inovyn to have better visibility of actions and to track the solutions until they are implemented.
Throughout the implementation process, Inovyn could balance their input with our advice and industry knowledge. Specialists from TenForce did regular check-ups with the decision makers from Inovyn, during several face-to-face meetings.
Getting a comprehensive view of actions from various sources couldn’t be simpler with TenForce Action Management. Actions are characterized by ‘who’, ‘what’, ‘when’, ‘source’, ‘priority’, ‘department’ etc. One core feature that Inovyn appreciates is the integration with other activity areas (shift logs, audits, maintenance tasks, etc.) and the fact that employees can easily export reports, based on the selected criteria.
In 2016, the adoption of the Management of Change (MoC) module came naturally and the process of change is much easier than during the period when Inovyn was using a system only for the engineering part of their workflow. First, a light version of the MoC module was tested and then a customized version of the solution was developed and set up. The best part was that TenForce’s experts integrated the old database into the new platform and now Inovyn has everything in one place.
Inovyn chose TenForce because our company could easily set up the workflows the organization needed. They also liked the flexibility of the screens, as compared to the previous rigid systems. Graphical dashboards and reports provide real-time visibility into the MoC process, enabling our client to proactively identify and address gaps, risks, and issues. Also, they were happy to see that there is an e-mail system incorporated in our solution, which is alerting all the people involved, all through the processes or change plans.
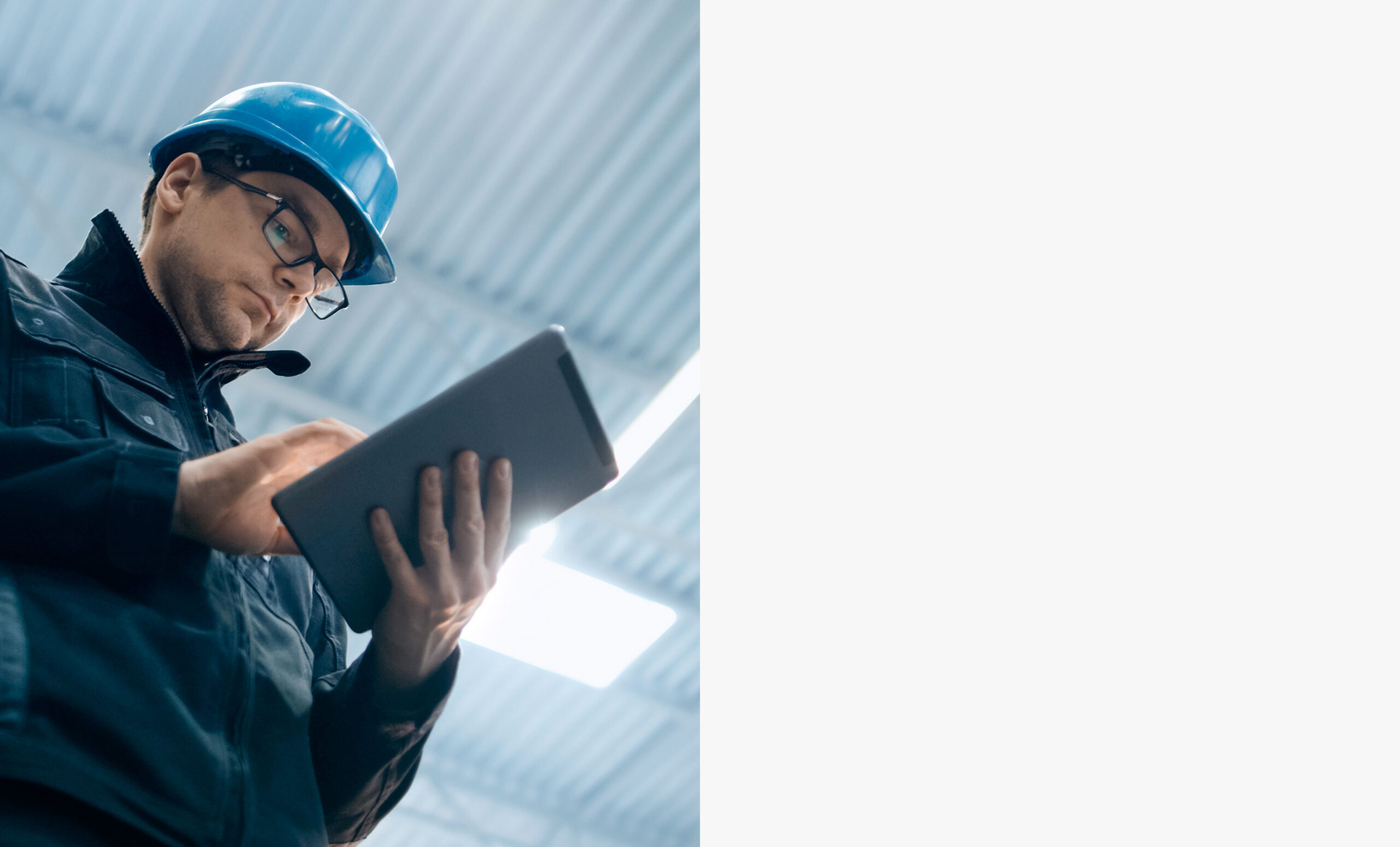
The Results Simply Followed
10 seconds to report an incident or near-miss event
All incidents and near-misses are now registered and nothing is forgotten. It only takes around 10 seconds for an operator to enter the necessary details in the customized system. As the forms are optimized and adapted to the company’s needs, TenForce is easy to use at all levels in the organization, after some training with the employees
The follow-up of actions has a better visibility
In TenForce, actions can be tracked and traced using ‘smart lists’ and creating and sharing them is now easily done at Inovyn. After registering the incidents, actions can be defined and notifications are set-up automatically. Key operators receive alerts periodically until the actions are marked as “done”. Employees also appreciate the built-in Excel generator that generates reports based on real-time data.
The management of change is now a seamless process
MoC requests are created via a checklist that reflects the impact of change on daily processes and production. Based on these checks, the change is evaluated and the necessary safety actions can be taken. Inovyn gains visibility over all change requests throughout the organization and the employees and the management staff are now sure that all steps are followed through configurable checklists. Also, the analysis reports contain trends and statistics that help Inovyn understand the hazard prone areas or processes.